Understanding Machine Bolts
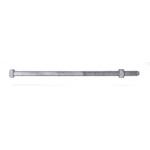
Machine bolts are a type of fastener that is used to join together two or more components like wood beams to utility poles, or metal brackets to steel columns, etc. They are available in a variety of types, sizes, materials, chemical treatments, and can be used in a wide range of applications on a ropes course or zipline structure.
One of the most important factors to consider when choosing a machine bolt is the grade. The grade of a machine bolt indicates its strength and performance and a specific grade may be called out by standards, regulations or engineering criteria. The higher the grade, the stronger the bolt.
Some of the most common grades of machine bolts include:
- A307: This is a general-purpose grade that is suitable for most applications.
- A325: This is a high-strength grade that is used in applications where high strength is required.
- Grade 8: This is a very strong grade that is used in applications where extreme strength is required.
In addition to the grade, there are a number of other factors to consider when choosing a machine bolt, such as the size, the head type, and the material.
The size of the machine bolt is important because it must be able to fit through the holes in the materials that are being joined together (typically 1/16" to 1/4" larger in diamater than the bolt). The head type of the machine bolt is also important because it must be able to fit into the space that is available, allowing the use of a impact wrench, torque wrench, linesman wrench or other tighening tool. The material coating of the machine bolt is also important because it must be able to withstand the environment in which it will be used. Corrosion resistant fasteneres are required for challenge courses and ropes courses that are outdoors and exposed to various wheather conditions.
Machine bolts can be treated with a variety of coatings to improve their corrosion resistance. One of the most common coatings is galvanization. Galvanization is a process that coats the bolt with a layer of zinc. The zinc layer protects the bolt from corrosion by forming a barrier between the bolt and the environment. Hot dipped galvanized bolts are the most common and offer the best protection. Simple zinc plating while corrosion resitant does not offer the same levell of protection as hot dipped galvanization. Stainless steel is another coating option and may be required in salt water enviornments like ropes courses built on or near a beach. Its important to note that stainless steel is more brittle than other coated metals nad typically need to be upsized for strength.
Here are some additional tips for choosing the right type of machine bolt for your application:
- Consider the load that the bolt will be subjected to. The higher the load, the stronger the bolt must be. When in doubt check with a qualified professional like an engineer or professional ropes course designer or installer.
- Consider the environment in which the bolt will be used. If the bolt will be exposed to corrosive elements, such as salt water or chemicals, you will need to choose a bolt that is corrosion resistant. In some marine applications Stainless steel bolts may be required.
- Consider the cost of the bolt. Machine bolts can range in price from a few cents to several dollars. Choose a bolt that fits your budget.
- Dont forget the nuts and washers (round, square, ogee, lock washers, double coil lock washers, etc.